میتوان لوله مانیسمان (بدون درز) را بر اساس روشهای مختلف تولید به دستههای لوله مانیسمان نورد گرم، لوله مانیسمان نورد سرد، لوله مانیسمان کشیده سرد و لوله مانیسمان اکسترود شده تقسیم کرد. با این مقاله از سلسله مقالات لوله مانیسمان پترو ایلیا انرژی همراه ما باشید.
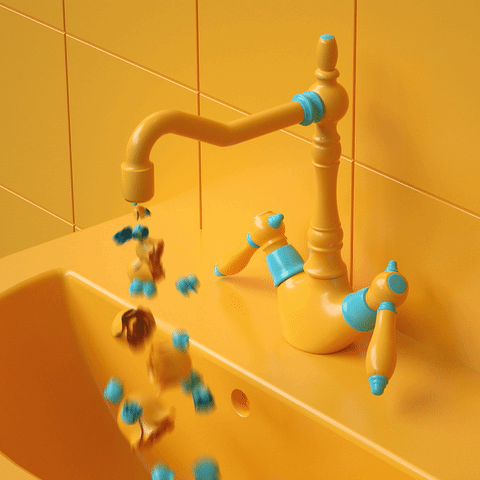
به دنبال کاملترین خدمات هستید؟
ما با بهروزترین تجهیزات و محصولات در کنار شما هستیم. برای دریافت مشاوره در انتخاب و خرید تجهیزات میتوانید، همین حالا با ما تماس بگیرید.لوله مانیسمان نورد گرم عمدتاً توسط دستگاههای نورد اتوماتیک تولید میشوند. در فرآیند تولید این لوله ابتدا بیلت مورد بازرسی قرار گرفته و نواقص سطح آن برطرف میشود. سپس بیلت به اندازههای مورد نیاز بریده شده و به داخل کوره فرستاده میشود تا حرارت ببیند. سپس بیلت وارد دستگاه پانچر شده و سوراخکاری میشود. به طور همزمان سوراخکاری به طور پیوسته و چرخشی ادامه پیدا کرده و به تدریج حفرهای درون بیلت ایجاد میشود که به آن تیوب مویی میگویند. سپس لوله وارد دستگاه نورد میشود. در آخر از دستگاهی جهت دستیابی به ضخامت دیواره یکسان استفاده میگردد. وظیفه دستگاه سایز کننده لوله ایجاد قطری مطابق با نیازهای مشتری است. در میان همه روشهای تولید لوله مانیسمان، روش تولید لوله مانیسمان نورد گرم با استفاده از دستگاه نورد پیوسته پیشرفتهتر میباشد.
اگر تولید کننده قصد داشته باشد تا لوله مانیسمانی با سایزهای کوچکتر و کیفیت بهتر تولید کند باید از روش نورد سرد یا کشش سرد و یا ترکیبی از این دو استفاده نماید. نورد سرد معمولاً توسط دستگاهی دو غلتکه انجام میشود که طی این فرآیند لوله درون یک حفره حلقوی نورد میشود. این حفره حلقوی از حفرهای مدور با سطح متغیر و یک سری ثابت مخروطی تشکیل شده است. کشش سرد معمولاً بر روی دستگاه کشش سرد تک یا دو زنجیره انجام میشود.
در روش اکستروژن بیلت گرد پس از حرارت دیدن داخل یک سیلندر اکستروژن بسته قرار گرفته سپس لوله دستگاه سوراخکاری و لوله اکستروژن به طور همزمان کار خود را آغاز کرده و تا قالب را از حفره کوچک خارج کنند. با این روش میتوان لولههای فلزی با ضخامت کمتر تولید کرد.
مواد اولیه برای تولید لوله مانیسمان فولادی (بیلت گرد)
معمولاً برای تولید بیلتهای گردی که مواد اولیه لوله مانیسمان به شمار میروند از روش ریختهگری مداوم استفاده میشود. سوراخکاری بیلت گرد به دو غلتک شیبدار وابسته است که بیلت گرد را میچرخانند و به سمت انتهای مندرل پیش میبرند. سوارخکاری سطح داخلی بیلت در واقع دیواره داخلی لوله فلزی مانیسمان را میسازد که این فرآیند بسیار خشن است. نیازمندیهای کیفی برای بیلت گرد ازین قرارند:
۱- تراکم مرکزی خوب و کم بودن بزرگنمایی در ساختار. اگر در مرکز بیلت شُلی یا ترک خوردگی وجود داشته باشد علائم ترک بر روی سطح داخلی لوله فلزی مانیسمان باقی خواهند ماند. تراکم ناحیه شُل با تراکم ناحیه سطح لوله فرق دارد (مانند cm3/0.005~0.003) در نتیجه هنگامی که لوله دچار فرسایش شود با ضایعاتی ترک خورده مواجه خواهیم شد.
۲- بیلت گرد باید از کیفیت سطح خوبی برخوردار باشد. اگر سوراخی سطحی یا ضایعهای کوچک بر روی سطح بیلت وجود داشته باشد به احتمال زیاد لوله در اثر سایش دچار شکاف و شکستگی شده و ترکهایی بر روی سطح آن پدیدار خواهد شد.
۳- خلوص بیلت گرد. اکنلوزیون در ۱۳ میلیمتر از بیلت و انکلوزیون ذرات بزرگ داخلی بیلت دلیل اصلی وقوع ترک در لوله میباشند. در یکی از نمونههایی که ما در اختیار داشتیم میزان انکلوزیون کمتر از %۰.۰۳۵ بود بنابراین میزان ضایعات تا حد زیادی کاهش یافت.
۴- اگر ترک داخلی بیلت گرد جدی باشد، نمیتوان لوله را جوش داد.
۵- بیضوی بودن بیلت. ناهموار شدن سطح بیلت به دلیل عدم خنکسازی یکدست لوله رخ میدهد و همین امر باعث بیضوی شدن شکل لوله مانیسمان میگردد.
کریستالایزرهای بیلتهای گرد بر خلاف کریستالایزرهای بیلتهای مربعی، دارای گوشههای پیش جامد نیستند که این باعث خنک شدن یکدست کریستالایزر و ناحیه خنک کننده ثانویه میشود، بنابراین پوسته به صورت یکسان منقبض شده و از بیضی شدن شکل لوله و به وجود آمدن ترک در سطح آن جلوگیری میشود. جهت اطمینان از کیفیت بیلت گرد تکنیکهای موثری برای ریختهگری مداوم وجود دارند مانند کنترل تمامی فرآیند ریختهگری، کنترل فرآیند خنکسازی ثانویه، تاندیش با ظرفیت بالا، کنترل خودکار سطح مایع، استفاده از تکان دهنده الکترومغناطیسی و … .
با توجه به توسعه صنعت تولید فلزات فرآیند تولید نیز پیشرفت زیادی داشته؛ تکنولوژی ریختهگری مداوم، و آخرین تکنولوژیهای صنایع الکترونیک و کنترل اتوماسیون در ریختهگری مانند حرارتدهی تاندیش، انرژی الکتریکی کریستالایزر (تکنولوژی ارتعاش غیرسینوسی)، کنترل خودکار سطح مایع، تکنولوژی کنترل محصول و تکنولوژی کنترل برای قرار دادن مایع فولاد ذوب شده در تاندیش همگی در بهبود کیفیت ریخته گری مداوم تاثیر زیادی داشتهاند.
در عین حال چون یکی از بزرگترین ویژگیهای فرآیند اکستروژن بهبود قابلیت شکل پذیری مواد اولیه است در واقع میتواند موقعیت خوبی را برای انجام ریختهگری مداوم ایجاد نماید. در حال حاضر روش ریختهگری مداوم در بسیاری از کارخانهها مورد استفاده قرار میگیرد.
در بحث پیرامون این مقاله شرکت کنید!