ظهور فناوری غلتک صنعتی و پیشرفت آن در اوایل قرن ۱۸، صنعتی شدن ساخت لوله را نوید داد. در ابتدا نوارهای صافشده ورقه فولاد، توسط قیفها یا غلتکها به شکل لوله در میآمدند، سپس سر یا ته آنها را در همان دما به هم جوش میدادند (فرآیند جوشکاری فورج). با این مقاله از سلسله مقالات لوله مانیسمان پترو ایلیا انرژی همراه ما باشید.
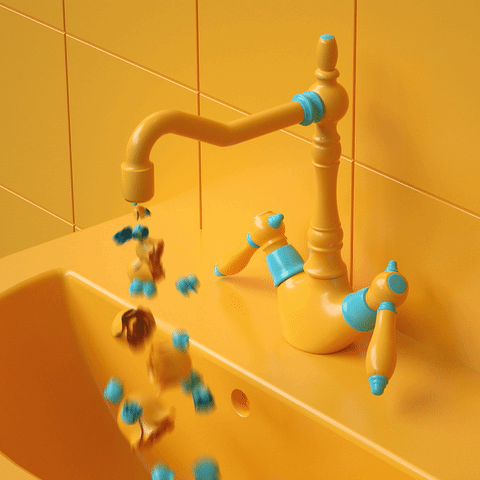
به دنبال کاملترین خدمات هستید؟
ما با بهروزترین تجهیزات و محصولات در کنار شما هستیم. برای دریافت مشاوره در انتخاب و خرید تجهیزات میتوانید، همین حالا با ما تماس بگیرید.با پایان قرن ۱۸، همزمان با افزایش شدید کمیت تولید در یک مقطع زمانی کوتاه، روشهای زیادی برای ساخت لوله مانیسمان به وجود آمد. با وجود دیگر فرآیندهای جوشکاری، توسعه جاری و پیشرفت تکنیکهای ساخت لوله مانیسمان، در نهایت لولههای درزدار (جوشکاری شده) کاملاً از بازار حذف شدند، و این سلطه لوله صنعتی مانیسمان بر بازار تا جنگ جهانی دوم ادامه داشت.
در دوره بعدی، در نتیجه تحقیقات صورت گرفته در زمینه فناوری جوشکاری، لولههای درزدار برای باری دیگر با قدرت به بازار بازگشتند. این بازگشت موجب آغاز توسعه صنعت لولههای درزدار و پدید آمدن شیوههای جدید ساخت لوله درزدار گردید.
اکنون چیزی حدود دو سوم تولیدات لوله فولادی در جهان، بر اساس فرآیندهای جوشکاریمحور است. با این حال، چیزی حدود یک چهارم لولههای درزدار، به شکل لولههایی قطر-بزرگ با گستره ابعادی ساخته میشوند که استفاده از لولههای مانیسمان در آن ابعاد مقرون به صرفهتر بوده و این لولهها جایگاه بهتری در بازار ساخت لوله دارند.
لوله مانیسمان
اکثر روشهای ساخت لوله مانیسمان در اواخر قرن ۱۹ به وجود آمدند. با منقضی شدن انحصار تولید و حق مالکیت، روشهای تولیدی که به صورت موازی در ابتدا اجرا میشدند، وجه تمایز و منحصر به فرد بودنشان را از دست داده و به مرور با روشهای دیگر ادغام شدند. امروزه وضعیت تولید این محصول به سطحی از توسعه رسیده است که اولویت با فرآیندهای اجرایی مدرن ذیل است:
فرآیند پرطرفدار دستگاه مندرل و فرآیند “پوش بِنچ” در محدوده ابعادی ۲۱ تا ۱۷۸ میلیمتر در قطر خارجی.
دستگاه پلاگ چند پایه با سنبه مندرل شناور تحت کنترل و فرآیند دستگاه پلاگ در محدوده ابعادی ۱۴۰ تا ۴۰۶ میلیمتر در قطر خارجی.
فرآیند غلتک سوراخکاری و فرآیند “نوردِ پیلگر در محدوده ابعادی ۲۵۰ تا ۶۶۰ میلیمتر در قطر خارجی.
فرآیند دستگاه مندرل
در فرآیند دستگاه مندرل از یک شمش استوانهای فولاد برای ساخت لوله صنعتی مانیسمان استفاده میشود. در ابتدا در یک کوره چرخان به شمش گرما داده شده و سپس توسط دستگاه سوراخ میشود. سپس به شمش سوراخشده توسط غلتکهای دستگاه مندرل شکل داده شده تا ضخامت دیواره و قطر خارجی آن کاهش پیدا کند.
بدینگونه به لوله مادر با طول چندگانه میرسیم. لوله مادر دوباره مورد گرمادهی قرار گرفته و سپس حجم آن توسط دستگاه به ابعاد مشخصی کاهش مییابد. در آخر پس از سرد شدن، لوله برش خورده، صاف شده و زوائد سطح آن حذف میشود. اکنون کار تولید لوله به تمام رسیده است. حال فقط باید مورد بررسی نهایی قرار گیرد تا آماده ارسال شود.
فرآیند مانیسمان دستگاه پلاگ
در فرآیند دستگاه پلاگ هم مانند فرآیند دستگاه مندرل، همه چیز از یک شمش استوانهای فولادی شروع میشود. شمش به طور یکپارچه در یک کوره چرخان داغ شده و سپس توسط دستگاه سوراخکاری مانیسمان، سوراخ میشود. حجم بدنه اولیه به دست آمده، به اندازه قطر خارجی و ضخامت دیواره مورد نظر تقلیل مییابد.
سطح درونی و بیرونی بدنه لوله به طور همزمان توسط یک دستگاه چرخنده صیقل میخورد. لوله صیقل خورده توسط دستگاه سایزینگ به ابعاد مورد نظر در میآید. لوله از این مرحله به بخش صاف کردن سطح لوله فرستاده میشود. این فرآیند با گرمادهی نهایی به پایان میرسد. لوله پس از اینکه مورد بررسی قرار گرفت، تبدیل به محصول نهایی میشود.
لوله درزدار
از وقتی که بشر قادر به ساخت ورقه و نوارهای فلزی شد، در تلاش بوده که کنارههای ورقه را خم کند و آنها را جوش بدهد تا بتواند لوله بسازد. این روش قدیمیترین فرآیند جوشکاری محسوب میشود، یعنی فرآیند جوشکاری فورج، که قدمتی ۱۵۰ ساله دارد.
در سال ۱۸۲۵، جیمز وایتهاوس، تاجر آهنآلات، امتیاز تولید لوله درزدار را به دست آورد. فرآیند تولید این لولهها شامل کوبیدن و شکل دادن قطعات مجزای فلز به دور یک میله برای ساخت لولهای با درز باز بود، سپس کنارههای مقابل هم را گرما داده و با پرس کردنشان به یکدیگر، آنها را به هم جوش میدادند.
با پیشرفت فناوری ساخت و جوشکاری لولههای درزدار به حدی رسید که فقط یک طرف لوله را در کوره جوشکاری قرار میدادند و لوله را میساختند. توسعه این شیوه جوشکاری در سال ۱۹۳۱، با فرآیند “فرتس-مون” به اوج خود رسید. این فرآیند توسط “جِی. مونِ” آمریکایی و همکار آلمانی اش، “فریتز”، ابداع شد.
این روش همواره تا امروز برای ساخت لولههایی با قطر حداکثر ۱۱۴ میلیمتر، موفق بوده است. در کنار این تکنیک جوشکاری، که نوار در کوره به قدری حرارت میبیند تا به دمای جوشکاری برسد، چندین روش دیگر از سال ۱۸۸۶ تا ۱۸۹۰ توسط “ای. تامسون” آمریکایی ابداع شد. این روش شرایطی را فراهم میکرد که در آن فلزات بتوانند به صورت الکتریکی به یکدیگر جوش بخورند. سنگ بنای این روش توسط یکی از اختراعات “جیمز پی. جول” گذاشته شد. این اختراع یک جریان الکتریکی را از خود عبور میداد و به کنداکتور میرساند، کنداکتور بر اثر مقاومت الکتریکی داغ میشد و جوشکاری صورت میگرفت.
در سال ۱۸۹۸ در آمریکا، شرکت ابزار استاندارد امتیاز جوشکاری با مقاومت الکتریکی برای تولید لوله را به دست آورد. تولید لولههای ساخته شده با روش جوشکاری الکتریکی، نخست در آمریکا و سپس در آلمان افزایش قابل توجهی یافت. این در حالی بود که تولید انبوه لوله مانیسمان فولادی با فرآیند دستگاه مندرل نیازمند حجم زیادی از مواد اولیه بود. در جریان جنگ جهانی دوم، فرآیند جوشکاری آرکِ آرگون، باز هم در آمریکا ابداع و در جوشکاری منیزیم برای ساخت و ساز هواپیما بسیار کارآمد واقع شد.
در نتیجه این دستاورد، فرآیندهای بسیاری با استفاده از جوشکاری گازمحور، برای ساخت لولههای فولادی ضدزنگ به وجود آمد. ساخت خط لولههای طولانی با ظرفیت بالا، حاصل پیشرفتهای بزرگی بود که در زمینه انرژی در ۳۰ سال اخیر رخ داد و در نتیجهی ساخت خط لولههای عظیم، فرآیند جوشکاری زیر آب از اهمیت زیادی برای خط لولههای با قطر بیش از ۵۰۰ میلیمتر برخوردار شد.
دستگاه جوش الکتریکی لوله
نوار فولادی به عرض مورد نظر، از صفحه فولادی بریده میشود. سپس نوار به دور قرقره پیچیده شده و توسط غلتکهای شکل دهنده، تبدیل به پوسته اولیه لوله با طول چندگانه میشود. کنارههای نوار به طور مداوم توسط یک مقاومت القایی قوی به هم جوش میخورند. در ادامه لوله به صورت الکتریکی گرمادهی میشود. سپس لوله را اندازهگیری کرده و توسط یک ماشین معلق برش، به اندازههای مورد نظر بریده میشود. نقاط برش در هر دو طرف صاف شده و صیقل میبینند. این فرآیند با بررسی فراصوتی و آزمایشات هیدرو استاتیک، به پایان میرسد.
در بحث پیرامون این مقاله شرکت کنید!